My career has spanned through the four major types of automotive ignition systems:
• Conventional breaker-point (mechanical) ignitions
• High energy (electronic) ignitions - HEI
• Distributor-less (waste spark) ignition
• Coil-on-plug (COP) ignition, which uses redesigned ignition coils that sit directly on top of the spark plugs, no more plug wires.
The purpose of the ignition system is to create a high voltage spark at the correct time and at the required intensity. The ignition coil is a major player in the system. Its job is to take 12 volts and turn it into kilovolts (KV or thousands of volts) to jump the gap at the spark plug.
When a current flows through a coil of wire, it creates a magnetic field around the coil. The magnetic field is effectively a store of energy, which can then be converted back into electricity.
If a coil of wire is exposed to a magnetic field and it changes, it creates an electric current in the coil of wire. This process is known as ‘inductance.’
If the current to the coil is switched off, the magnetic field will collapse and induce an electric current into the coil.
If two coils of wire are placed around each other and current is used to create a magnetic field around one coil (primary winding), it will also surround the second coil (secondary winding). When the electric current is switched off and the magnetic field then collapses, it will induce a voltage into both the primary and the secondary windings as high as 400 volts in the primary ignition and 18,000 to 40,000 (18KV to 40KV) in the secondary ignition.
Send that 40KV across a spark plug and we have ignition.
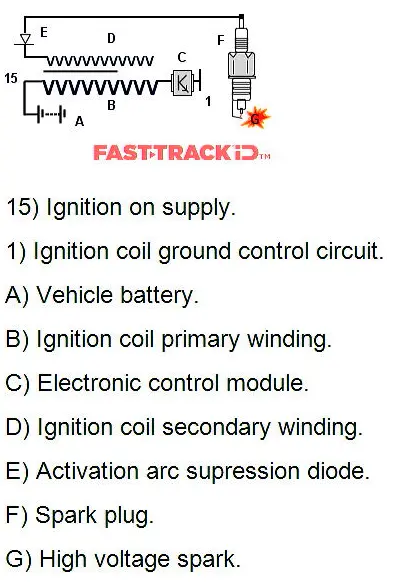
On a conventional ignition system, points were used to turn the current on and off. Today, COP systems utilize cam and crank sensors to signal a module to turn the current on and off.
On these modern systems the powertrain control module (PCM) can set codes for engine misfires. P0301, P0302, P0303, P0304, P0305, P0306, P0307 and P0308 all represent misfires on cylinders one through eight. P0300 is a random misfire from cylinder to cylinder, fuel volume/pressure issues or vacuum leaks might cause a random misfire, for example. These misfire codes can point you in the right direction then pinpoint testing would be the next step.
Below shows the optional COP 11 adapter that allows the ZEUS® to test secondary ignition.
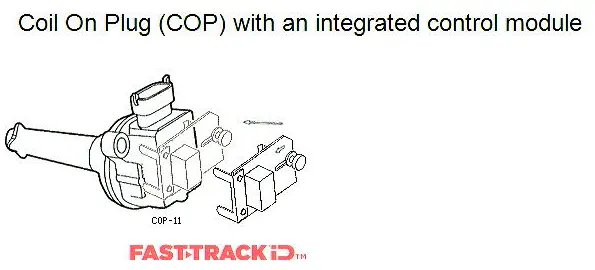
When we go to guided component tests and take a class on secondary ignition, we learn about how to use the firing section of the scope pattern to spot ignition misfires.
The firing section consists of the firing line and the spark line. The firing line is measured in KV and is how much voltage to jump the plug gap. The spark line shows how much voltage it takes to maintain the spark and displays the burn time.
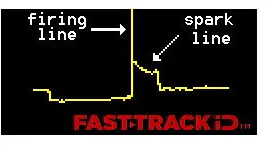
The spark line and burn time are affected by the gap and conditions in the cylinder like fuel mix or mechanical issues.
High firing line voltages indicates high resistance or lean air/fuel mix. Low lines could be a rich mix or low compression.
Another popular way to diagnose ignition issues is with a low current ramp test. By simply clamping the low amp probe around the primary power wire or fusible link, you will get a clear picture or current/amperage flowing through the circuit.
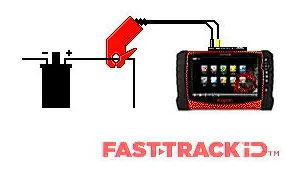
Coils may limit the current and have a flat top. Others have a sharp peak.
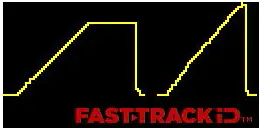
If the coil waveform has a sharp rise at the beginning of the ramp, suspect a shorted coil, as seen below.
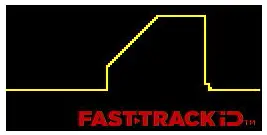
Ignition systems have been around since the beginning of internal combustion engines. Since their inception, ignition systems have been a leading cause of misfires and check engine lights. The key takeaway for this common issue is to be able to quickly and accurately diagnose those ignition problems.