Snap-on IM5 Impact Wrench
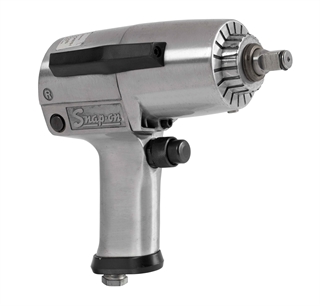
In the late 1940’s and the 1950’s the use and manufacture of air powered impact wrenches expanded. Snap-on contracted for production of the AW500, a very successful ½ inch impact so powerful it had a durability problem necessitating a change. Gene Olson, Snap-on product engineer, designed the IM5, then manufactured in the Natick plant and launched the IM5 in 1970, an important entry into this market.
Snap-on FAR7 Air Ratchet
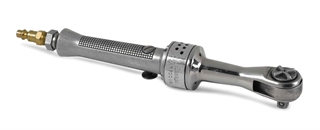
The FAR7 was the first air ratchet designed to apply the speed and torque of pneumatic power in close quarters, turning fasteners many times faster than by hand. Lightweight, but powerful, the ratchet also limited the torque applied to avoid stripping fasteners. A 1970’s dealer visit to a customer in Oklahoma revealed a local mechanic had invented and was locally manufacturing the first air powered ratchet. Snap-on purchased the patent rights and used them to design the first FAR7 air ratchet.
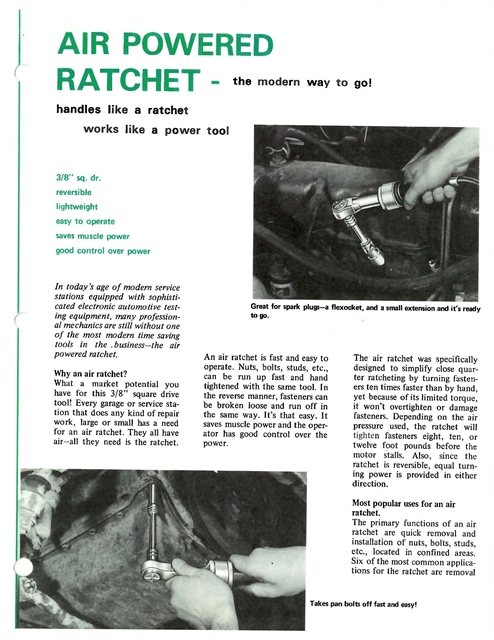
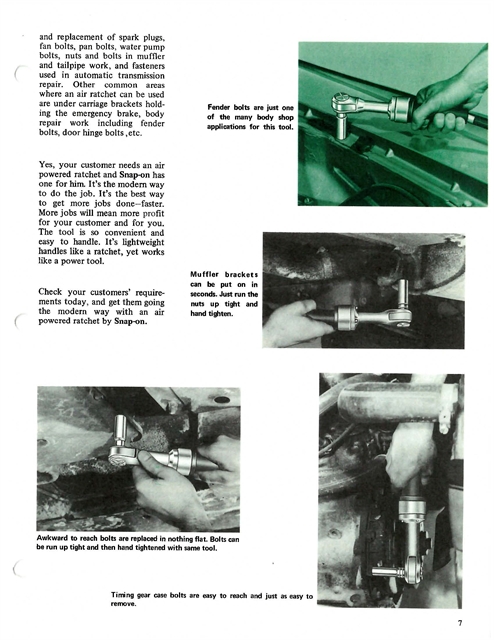
Snap-on Automated Tool Control (ATC)
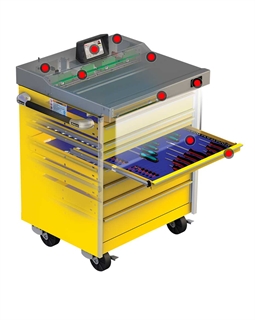
Snap-on Automated Tool Control (ATC) solutions offer the advantages of years of customer connection and engineering development. The digital imaging technology and proprietary software scan drawer or locker contents and record which tools are removed and replaced in real time, maintaining technician ability to operate at the speed of work. Launched in 2012, ATC now has a massive, global installed base.
Operating At the Speed of Work: Automated Tool Control
Managing tools in kits for specific applications is challenging. Operations want to deliver selected tools for specific tasks in both manufacturing and maintenance environments. Lost tools kill productivity and they can cause damage if lost in areas like the inside of an aircraft engine. Operations want to know who is using tools and how often they are used, serviced or calibrated. This requires an enabled solution.
These challenges exist across many critical industries. In aerospace and aviation, in oil and gas maintenance, in railroad and manufacturing, in nuclear plants and even in food manufacturing, there are needs for high-performance tool control.
Foreign object damage (FOD) costs millions of dollars a year in damage to equipment and personnel. The Snap-on ATC solution was created to eliminate the potential for human error during check-in, check-out, and tracking, giving it the highest levels of FOD compliance. Our solutioneers have daily, deep experience in some of the most challenging operations across the world.
The Snap-on Level 5 solution counters FOD in five ways: tool organization, visibility, and security, tracking and digital accountability. No tool goes unaccounted for, so managers know - in real-time - who's using which tools, where and when.
Snap-on engineers developed the original solution, then launched it in selected user environments. Users in those operations gradually contributed feedback and requests for improvements. We also spent time observing users at work to look for unmet needs and potential improvements.
The focus of these efforts has been to provide real-time solutions that move at the speed of work so technician productivity is enhanced.
Over several years, this customer connection process contributed a long series of product enhancements. Examples of these include:
- Tracking of serialized and calibrated items like torque wrenches
- Ability to manage and check out groups of related items using kits or “fast pads”
- Communication via email or text when tools are used or calibration is required
- User-defined graphic interface and customization for queries and report writing
- ANDON lights to alert user to important conditions
- Enhanced analysis, reporting and inventory tracking from administrator workstations
- Lockers for larger items coupled to advanced RFID technology to track tools
- Custom battery power system providing mobility and safe mode to prevent data loss
The ATC solution continues to succeed across multinational operations and many industries. From small operations using one or two boxes to highly developed and sophisticated operations using hundreds of ATC systems, it continues to grow and become more effective as features and capabilities are added.
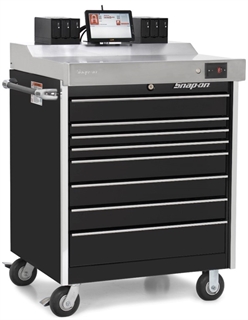
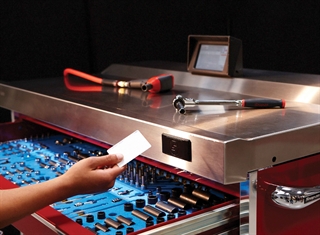
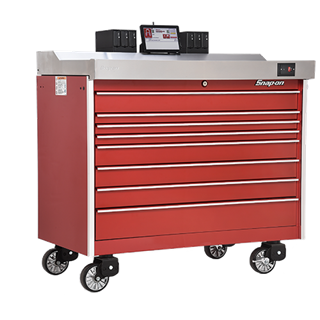
Snap-on Certification Kits
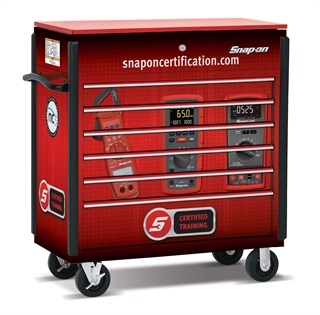
In 2007, along with partners from education and government, Snap-on recognized the need to provide standard training, testing and certification for students at technical colleges. Certification kits containing tools, lab materials, curriculum and instructor training were launched for diagnostics. In 2019, certifications are being offered in 16 product categories with 63 specific applications variations at 560 certification centers nationally.
Snap-on Counselor Digital Oscilloscope

Developed in the mid 1980’s, the Counselor offered a dramatic departure from previous designs. The compact engine analyzer provided the functionality of earlier, giant tune-up consoles (usually priced out of reach for all but a few technicians), in a portable package for one-seventh of the cost. It combined waveform, alphanumeric and bar graph analysis in one instrument.
Weighing only 40 pounds, it allowed technicians a portable way to diagnose engine problems by graphically displaying the operations involved in firing the cylinders. This included firing order, rpm, dwell, spark plug firing, ignition information and voltage, alternator, fuel injector and cylinder shorting information. It also offered a memory bank to store information for future reference.
Together, these features helped techs do the job quickly and correctly the first time. It was extremely versatile, with automotive, industrial, marine, aviation, recreation and farm applications. Manufactured in the Snap-on facility in East Troy, Wisconsin, it packed a testing and tune-up punch that revolutionized the industry.
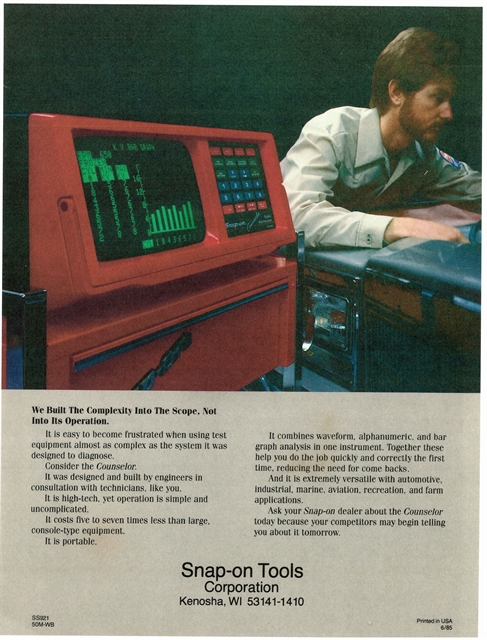
Snap-on Dual 80 Ratchet
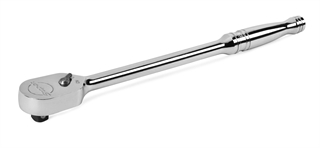
Offering over 110 ratchet sizes and configurations, Snap-on is the market leader in the tool that is directly descended from its first interchangeable ratchet in 1923.
The Dual 80 ratchet, launched in 2012 sustained these key elements. It continued to be a small tool with good fit for better accessibility in tight places. The sealed ratcheting mechanism permanently retains lubricant for peak operation, and it provides a high-polish, lustrous chrome finish.
The design offers several important improvements.
An 80-tooth mechanism replaced the 36-tooth mechanism used in the preceding 936 series ratchet. This reduced the amount of arc required to engage the ratchet by 25% while maintaining a small profile for accessibility. This makes the work more precise and easier for the technician.
It reduced the ratcheting effort required to spin the gear, facilitating one-hand operation. It does this by reducing ratcheting torque, the torque required to spin the ratcheting gear. This is particularly important when a fastener has broken loose but still must be unthreaded from its mating part.
The new design virtually eliminated self-reversal that sometimes occurs when a fastener breaks loose rapidly.
Snap-on EPIQ Tool Storage Platform
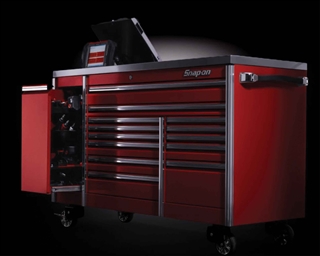
This tool storage solution was created by technicians for technicians, to meet their changing needs and launched in 2008. It features on-board, engineered power, a power drawer for charging tools, monster drawer load ratings, inpulse locking system and an iso-ride suspension system. It was at the heart of relaunching tool storage and reasserting Snap-on differentiation.
Snap-on storage systems were lagging behind the times and customers let us know how they felt. We visited hundreds of customers in dozens of shops across multiple industries to understand how products were used, what was missing, what was working. The design team established which of Snap-on’s core manufacturing and product design features were prominent, competitively superior and key differentiators. These findings resulted in mockups that were shown to customers and compared to competitors. We invited the customers to try the products and offer feedback. Then we took that feedback and developed a wide range of new features and designs. The result was a new line that solved real customer challenges in a new design that was easy to use and offered attractive, useful and interactive touch points.
Later, the platform was expanded to include more options and configurations. Several of the new features developed via customer observation and input were migrated into other Snap-on tool storage platforms.
Snap-on Flank Drive
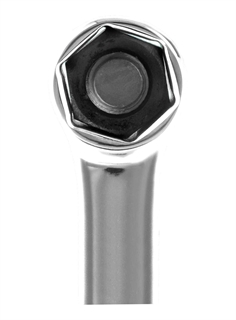
Patented in 1966, was the most significant design change in the Snap-on line since the original interchangeable “5 do the work of 50” invention that started the company.
As jet aviation grew in the 40’s and 50’s, smaller, harder fasteners were needed to reduce weight. Jet engines for military aircraft, in particular, evolved during the Korean conflict in the 1950’s. One of the new features of these jet engines was the use of high-strength, 12-point fasteners. These nuts and bolts were made smaller and stronger to save weight and space. They were torqued to high levels and exposed to high temperatures.
Conventional 12 point tools worked satisfactorily for assembly of jet engines but proved to be inadequate for removal for service and repair. After the heat and corrosion and straps encountered in use, conventional tools often “rounded-off” the corners of the 12 point fasteners because of the high removal torque. Sometimes, they were so tight technicians broke tools when removing them. The US Navy Air Command was desperate for a solution and approached Snap-on with the problem in the early 1960’s.
Gene Olsen, a new mechanical engineer at Snap-on, had recently finished his master’s thesis on “Stress Analysis of the Hexagon Socket.” He had recently researched a lot of stress theory and analysis. Gene contemplated the problem and sketched out the Flank Drive idea in about 30 minutes, taking the next few days to calculate the angles and equations. He used this initial concept to develop the Flank Drive solution in which the socket was redesigned to contact the flat sides of fasteners and protect the corners.
In 1965, Snap-on received patents on Flank Drive® an innovative wrenching design that revolutionized the way nuts and fasteners were removed without rounding off the corners.
After success in solving this problem for the military, Snap-on recognized the potential benefit to users across many industries and changed the entire product line to Flank Drive.
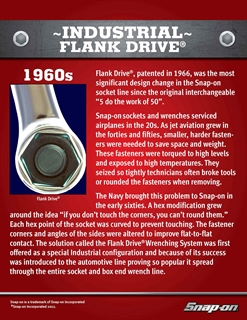
Snap-on Flank Drive Extra
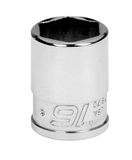
In 2018, Snap-on improved Flank Drive with Flank Drive Extra (FDX) on sockets, which grips fasteners further off the corner, offering 25% higher strength and a 50% increase in turning power with damaged fasteners. Invented by engineer, Dan Eggert, the patented geometry of the FDX socket greatly improves the user’s ability to get the job done efficiently.
The reimagined Flank Drive® Xtra (FDX™) socket system is the first socket redesign in more than 50 years for one of the industry's most frequently used tools
Five standout benefits make the FDX unique from any other sockets:
- Small but mighty: in an improved design that grips fasteners further off the corners, the FDX offers up to 25 percent more strength than Flank Drive® sockets
- Rounded corners, no problem: with its angled contour, the socket wall grips damaged fasteners more closely for 50 percent more turning power
- Upgraded shape: an optimally chamfered lip on both the hex and drive ends of the socket allows for a better grip and more turning power, especially for shallow-headed fasteners and fasteners with limited top clearance
- Efficiently engineered: FDX sockets feature grooved, grippable outer walls, a unique design feature that makes them easier to remove
- Easily identified: easier identification and improved readability are both achieved through large, distinctive markings on the socket exterior
Background Story:
Snap-on engineering was challenged to invent a way for spline sockets to meet both the MIL standard and the Aerospace standards for spline sockets and become the first company to provide that product. This meant the spline sockets had to meet the higher performance requirements of the MIL standard while also meeting the thin wall requirements of the Aerospace standard. This combination of higher strength for durability and thin walls for access offers great benefit to technicians.
This objective required the spline sockets to meet a specific geometry with tolerances attributed to individual characteristics and still be able to turn all aerospace spline fasteners.
Spline sockets tend to fail by means of the spline teeth shearing off at the base. To improve strength, the material profiles of the spline geometry were analyzed using Finite Element Analysis. Modifications were made within the dimensional requirements of the spline socket standards and resulted in meeting the performance requirements of both standards. Although the sockets were already made of an aircraft quality steel, in order to allow all sizes of sockets in the standard set to meet the requirements, a higher grade Nickel alloy material was used.
The spline socket improvements were the catalyst to incorporate geometry changes into twelve point sockets. The geometry changes moved the contact point between socket and fastener further away from the corner to aid in removing fasteners that have rounded corners. Then, changes were applied to the six point socket geometry. The combination of changes significantly increased the strength of the sockets. The secure fit of the socket onto the fastener and the contact point moving slightly further from the corner of the fastener greatly improved the technician’s ability to get their job done more efficiently.
Snap-on Flank Drive Plus
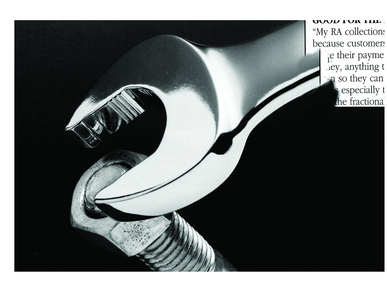
In the late 1980’s, Snap-on engineers sought to make Snap-on wrenches the strongest on the market. During their work, they found a design that revolutionized wrench design. Using finite element analysis enabled them to pinpoint where and how torque is applied, they found that the hard metals used to test wrench strength dug into the softer metal used to make competitive wrenches. As a result, the wrench turned slightly, shifting its force to the sides of the fastener. The wrench was being damaged in the process. This was a valuable discovery and no one had invested in the research to understand it before.
Soon, a team from engineering, manufacturing and marketing were working to translate the discovery into a new design. Snap-on created a new inside face configuration for its open-ended wrenches to transfer torque to the sides of the tool. To give the wrench the “tight” feel needed to win market acceptance, manufacturing needed to be able to produce wrenches within tolerances of two human hairs – precision never before attempted for a hand tool. Snap-on solved this and many other design and manufacturing challenges and created a significant wrench innovation.
In 1990, Snap-on introduced Flank Drive Plus, a new, patented wrench configuration that accomplished the same objective as Flank Drive did for sockets. It provides an average of 40% more turning power while protecting the fastener.
Snap-on Intelligent Diagnostics
Snap-on Level 5 Tool Control
Tool Control solutions are essential in a wide range of critical industries to keep track of, manage and identify tools. Foreign object damage is a major concern across many operations and productivity and retention are central to all. Snap-on began kitting for specific applications in the early 1920’s and the importance of value-added solutions has grown each day since that time.
Snap-on Level 5 Tool control offers proprietary, customer-designed, custom productivity solutions that address organization, visibility, access control, asset management and automation. These are the five levels of control and security offered by the systems in this solution. These benefits are delivered across thousands of tool storage configurations, kitting solutions, tool identification methods, access solutions, software programs and tool inventory management.


Snap-on MT2500 Scanner
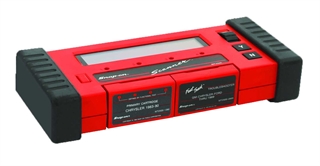
This new, compact scan tool revolutionized diagnostics in 1989 with complete messages, trouble code definitions and easy-to-read information, the industry’s first plain English system for checking hundreds of engine parameters.
In the late 1980’s engineers from Balco, a wheel alignment specialist company that was acquired by Snap-on, worked closely with automotive technicians to create the compact, hand-held device known as the first Snap-on Scanner. It was designed to access engine control computers on vehicles.
The first of these tools became available in 1989 for domestic vehicles and Asian troubleshooters followed in 1991. They also turned their efforts toward developing a transmission tool. Their approach was unique. They wanted to develop a tool that was designed by working technicians for working technicians.
They said: “We were going to build something they wanted and would contribute to right from the beginning…..Ease of use and very few controls were also important….we came up with the concept of a scrolling wheel that you use to find the information.
Chief engineer Keith Kreft, explained further, “Capturing the real experiences, the real problems and disseminating that information were the principles behind the scanner.
A series of cartridges made it possible to update information, offered additional makes, models and troubleshooter applications. Years of enhancements simplified complexity and added speed and efficiency to repairs. Kreft explained; “whatever new things we learn will be built into new cartridges that will fit in the scanner. The result was a series of significant advances and innovations enabling automotive technicians to be increasingly more effective in their work.
Snap-on Optical Toe Gauge
This equipment innovated alignment back in 1978 with a solution that provided fast setup, easy calibration, dual projection to independent wheels and an angle screen for easy viewing by technicians under the vehicle. It promised to save time and improve accuracy.
The lightweight unit was easy to handle and set-up and empowered thousands of technicians in shops across the world. An early milestone for Snap-on in the undercar equipment business, it set the stage for continued innovations.
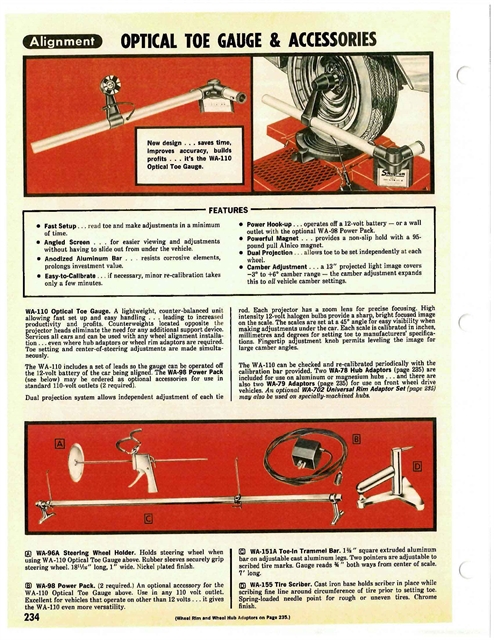
Snap-on Ratcheting Screwdriver
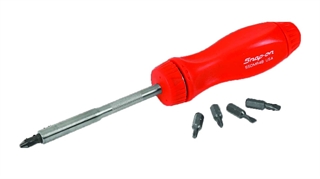
One of the most popular Snap-on tools ever was launched in 1987 after a major engineering and testing effort to ensure its performance, durability and flexibility. As an indication of its popularity, three years later, more than one million units were in the hands of excited professionals. Over the 33 years since, it has grown to be one of the top-selling Snap-on tools of all time.
The exciting design introduced in 1987 offered double the turning power of competitive units available at the time. It set a new standard for comfort and the ability to transfer power from palm to screw head. Within an internal zinc insert rested a patented ratcheting mechanism that distributes stress and force. But the ratcheting resistance is very low; the ratchet will operate with little drag on the fastener. The reverse cap was carefully designed so it could be operated with the thumb and index finger while still holding the handle in your hand.
The development effort included torture testing under extreme conditions: in searing heat and freezing cold, and with grit and dirt in the ratcheting mechanism. Engineers rotated the shank 200,000 times, operated the reverse cap 50,000 times and ran over the screwdriver with a vehicle.
Since that time, the original design has extended to include many different configurations suited to the specific needs of professional technicians. There are now 7 different handles and 7 interchangeable types of shanks available for unparalleled flexibility.
More recent versions provide a choice of hard handle or a soft elastomer handle for a firm, comfortable grip. Handle designs expanded to include stubby, long handle, and T-handle. The 5-position articulating handle features multiple locking positions with the push of a button.
The Transdrive ratchet mechanism is twice as strong as earlier versions.
Knurled shanks provide control and a small, high-strength Neodymium magnet retains bits and holds fasteners in place. It lasts longer than magnets found in ordinary screwdrivers.
The easy twist cap accesses bit storage for 10 bits with a quarter turn and a recess in the cap allows it to be used to turn fasteners in confined areas.
It has truly become a solution used across virtually every industry.
Snap-on SmartData
Snap-on SmartData is a software solution on Snap-on hand-held diagnostic tools. It automatically sorts through the massive amount of data streaming off of a vehicle to reveal only the ones that are out of spec or are specifically related to the areas specifically being serviced. The technician gets critical information in an easy-to-use manner that helps get cars fixed faster and more accurately.
SmartData was created from real fixes; it uses actual repairs done in shops that resulted in a successful fix. It searches a database of 1 billion fixes for the year, make, model and mileage of the vehicle being repaired. There are thousands of pieces of data streaming off of a vehicle. Voltages, pressures, on/off value, resistances…etc. SmartData looks for data values (fuel pump pressure, for example) that are either higher or lower than a known good range.
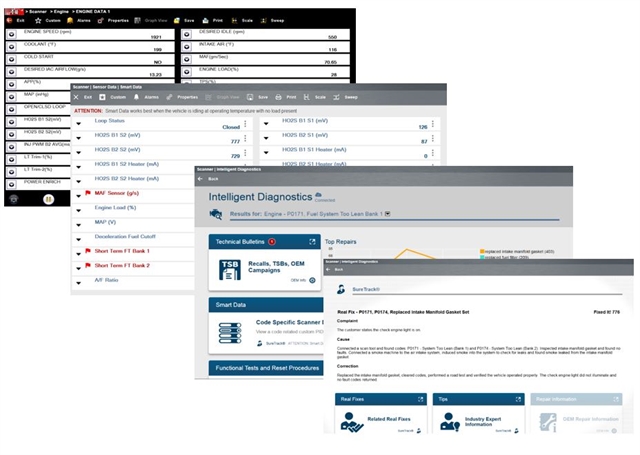
Snap-on Spline Wrench Design - 1960's
The introduction of Snap-on Flank Driveᶱ was prompted by the need for wrenching of 12-point, double-hex fasteners used on early jet aircraft engines. By the mid-1960s, military experience with 12-point bolt heads prompted the U.S. military to seek the “Optimum Design For Aircraft Structural Fasteners”.
The U.S. Naval Air Engineering Center in Philadelphia initiated a competitive process to find this “optimum design”. Tool companies and aerospace fastener manufacturers were asked to submit designated sizes of fastener designs and tool manufacturers were asked to submit sockets with corresponding high-strength wrenching designs. These designs were to be tested under prescribed conditions. Since this required submission of both fasteners and tools, most of the entries were fielded by an aerospace fastener company partnered with a tool company.
Snap-on partnered with the Elastic Stop Nut Corporation of America (ESNA) and submitted designs based on both manufacturability of the fastener and a high-strength wrenching design. The wrenching configuration was designed by Snap-on and 3 sizes of Snap-on sample sockets were made using high strength steel.
Seven different designs were entered by tool / fastener companies. These designs were tested by the U.S. Naval Engineering Center’s Aeronautical Materials Laboratory to determine the optimum wrenching configuration for high-temperature and high-strength aircraft fasteners. The Snap-on spline wrench design was judged to be the highest strength and most suitable design.
ESNA proceeded to produce high-strength spline fasteners and introduced them to aerospace companies and Snap-on began manufacturing and offering a range of spline tool sizes and configurations needed for manufacture and maintenance of these aircraft. Among the earliest applications were turbine blades on GE jet engines, airframe fasteners for the C-5 cargo planes, and U.S. Air Force F-16 and U.S. Navy F-18 fighter planes. Snap-on patented the design. Later improvements would continue to improve the design to meet advancing standards and inspire the development of the Snap-on FDX socket design.
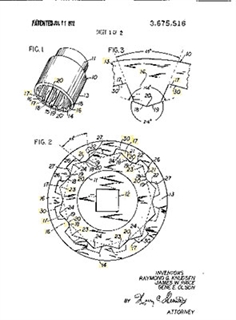
Snap-on Square Drive
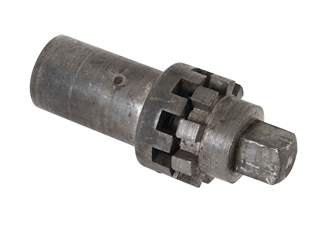
The initial size of the drive that enabled the “5 do the work of 50”set was ½ inch. This has remained a standard for over 100 years.
However, Snap-on soon recognized that smaller size sockets were needed to fit into tight spaces. Soon, the ¼ inch square “midget” line was launched. Similarly, heavy machinery required larger drive sizes and longer handles. The ¾ inch square and 1 inch square size handles and sockets soon followed.
The square drive of Joe Johnson’s sockets and Snap-on’s expansion of the square drive remains the standard in the world --- even for countries that otherwise use metric dimension tools.
Snap-on Stork Pliers
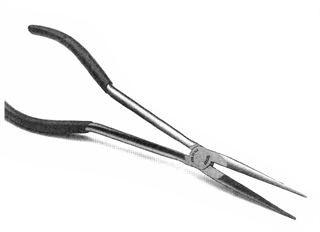
These very long-reach pliers were invented by Marshall Letson, a polisher in the Snap-on Mt. Carmel, IL plant. Introduced in 1991, they were one the world’s first professional quality long-reach pliers to solve accessibility problems. Extremely popular then and now, the original configuration was followed by variations to apply the reach to many more difficult-to-access situations.
Long-necked needle-nose pliers reach deep into narrow recesses to help pluck out, hold or align parts from areas a narrow as 3.4” and as deep as 6”. High strength alloy steel prolongs the life of the tool. Cushion grips provide control, comfort and extra gripping power.
A serrated, milled, gripping tooth design incorporates both a fine tooth and a coarser, angled tooth design. The fine tooth design is ideal for a wide range of general applications with the coarser design targeted for special applications where a maximum bite is desired.
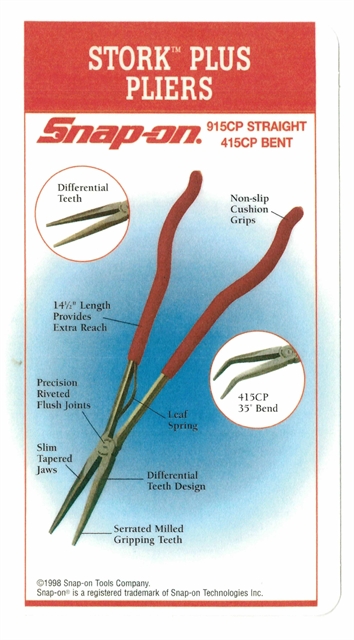
Snap-on TechAngle

First introduced in 2013 and recently updated in 2019, this breakthrough, flex-head torque wrench helps users achieve both specified torque force and angle measurements. The newest models are even more precise in flexed position due to Snap-on Multi Axis Gyro Compensation that allows the tool to measure its position and compensate for the change in length. Professionals using the TechAngle under a wide range of demanding circumstances especially appreciate the four alert modes the wrench provides – sequencing LED’s, LCD readout, vibratory feedback and audible signals.
This innovation demonstrates the combined roles of creative engineers, deep Customer Connection and patience over time. In 1993, Snap-on experimented with a new technology known as a piezoelectric gyroscope on torque wrenches. The technology was piloted among a group of professional users and it overcame the need for a user to remember a handle position and was thus more accurate. In 1996, a patent was issued to Snap-on. However, the cost and size of the sensor at the time was prohibitive.
In 2004, the price and size of the piezoelectric gyroscope had shrunk significantly. A team developed a new prototype angle measurement device. The unit would leverage microprocessor control for simplicity and size of operation. The test unit was a 1/2” drive extension with the measuring tool fitted around the central diameter. This tool was tested by technicians for feedback. They loved the concept, as the angle measuring tools of the time were cumbersome, slowing the repair process. They were concerned about the size of the prototype. The team considered a range of ways to clip onto a variety of socket extensions or the wrench body. In the end, the team chose the integrated torque and angle wrench as the concept to be pursued and the TechAngle was born.
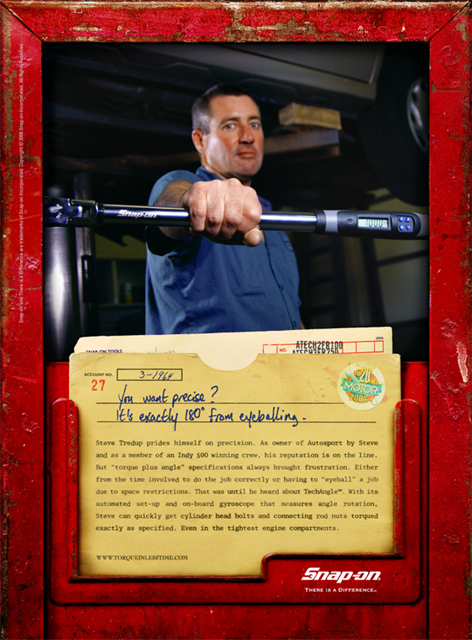
Snap-on Tool Storage Color Expansion
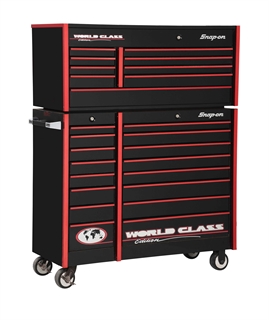
Paint Color Expansion in Tool Storage debuted in 1991, the first mass produced Snap-on offering of colors beyond “Kenosha Red.” The introductory edition sported gloss black paint accentuated by candy apple red trim. An instant success, the expansion of color offering led to the current offering of over 30 different colors with six trim color options.
Over time the ability to customize Snap-on tool storage has added a wide range of functional choices for users, with thousands of special features and configurations that help professionals design and select the right choice for their needs. Similarly, the development of high quality, custom wraps, lighting and other visual features have made it possible for companies and individuals to choose tool storage appearance that projects their individual passions and interests. Color and design deliver both functionality and personality.
Snap-on Torqometer
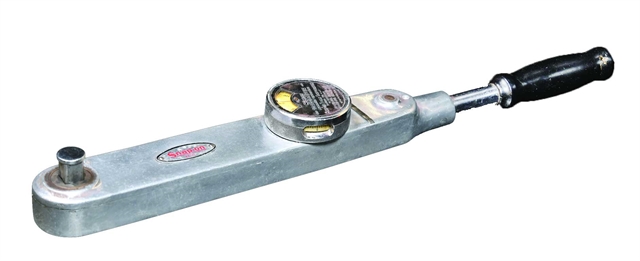
In the late 1930’s Snap-on responded to the need to take the guesswork out of applying torque with an exclusive agreement for a supplier to manufacture the TQ11 Torqometer®. Snap-on enjoyed a patented position, offering hit product for many years. In the 1980’s Snap-on designed and manufactured its own torque products, eventually welcoming several of the premier torque companies in the world into the Snap-on family.
The Torqometer is a tension measuring wrench. It is used to measure the amount of torque (twisting stress) necessary to overcome a given load. The Torqometer is a wrench and gauge combined; it is a precision instrument that insures accurate and uniform nut tightening.
Torqometers have been used in some of the most critical applications. Here’s a story from Paul Schutt, Eastern Division Manager in 1962. “I recently had a chance to talk with Charlie Allen, our Industrial salesman who calls on Cape Canaveral. He tells me that all the final adjustments on missiles, rockets, etc., are made with Snap-on Torqometers. He said that on a recent TV shot, when they were torqueing down the unit in which Colonel Glenn was going to be fired, you could see, on your picture screen, the Snap-on Torqometer being used. Let's let our customers know that Cape Canaveral is one of our best Torqometer customers.
Bahco Ergo Tool Management System (BETMS)
Bahco has introduced a state-of-the-art system that addresses specific customer needs with customization of tool storage and accessories, access control, kitting solutions and tool identification. A hallmark of the system is ease of design and development of kits. The process is simple:
Choose the right container with the tool selection you need.
Create the personalized portable working station you always dreamt to work more efficiently with the exact tool selection your business needs. It’s highly responsive, professional and does a great job. Select from a wide range of attributes and features you recognize from your work.
Organize. Increase efficiency and performance.
Our cutting edge Configurator software lets you personalize your tool storage management, deciding the container, the tool selection and the most important, how to organize them. Find the right tool, in the right position, at the right time!
Create a perfectly organized trolley with Fit & Go. The Fit & Go system contains a wide range of ready-to-use foam inlays with tools for your drawers.
Customize. Let your imagination fly. We will make it happen!
Use Online Configurator to start our tailor-made experience. We will guide you through an intuitive state of the art configurator. For additional configurations Bahco offers BETMS that will grant you all-round tailor-made configuration.
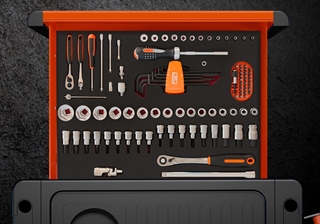
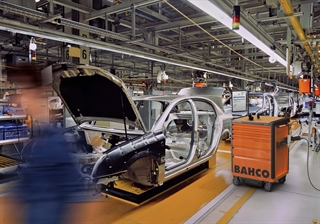
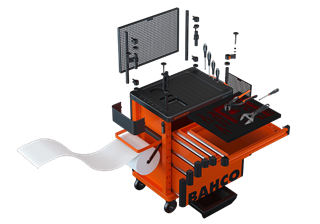
Learn more about Bahco
Bahco Hand Tools
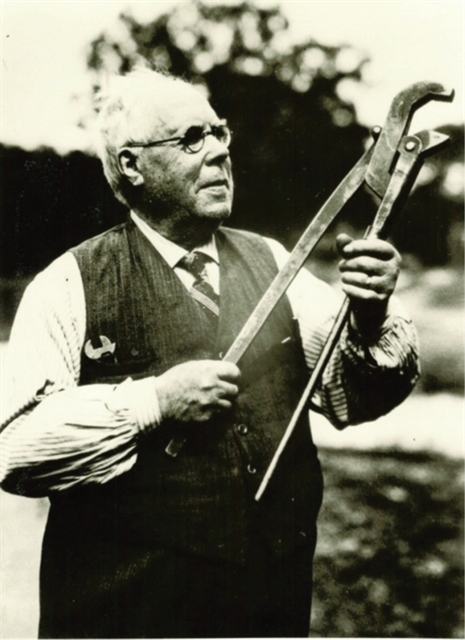
In 1862 Göran Fredrik Göransson founded Högbo Stål & Jernwerks AB, Sweden, and producing high quality steel using the Bessemer Process. In 1886 he started producing saw blades with the same high quality as the steel used to make high quality fishing hooks. The saws and tools were marked with the "Fish & Hook" brand as a symbol for the highest quality.
His company, which became Sandvik, acquired in 1999 by Snap-on, was the first to use the Bessemer method for industrial steel production. “Hard but Tough” was considered to be an insurmountable metallurgical task, but the Bessemer steel process had just the right special qualities and was ideal for the production of saw blades in 1886.
As the company grew, qualified labor was attracted by offering high wages and pleasant living conditions. Göransson spent a lifetime building the Sandviken Community that included gardens, new housing, an inn, healthcare, schools, and the Jernvallen top-level sports facility. Göransson’s was a visionary devoted to improving the work environment and the community where his employees lived and raised their families.
The very same year Goransson started his business, 1886, Johan Petter Johansson established Enköpings Mekaniska Verkstad in Enköping Sweden. J P Johansson was a clever and creative craftsman. Johansson’s idea was to replace fixed spanners with a single tool that would fit different sizes of bolts and nuts, much as the human hand functions. He became one of the foremost inventors in Sweden, holding 118 patents.
In 1888 Johansson received his first patent for “The Iron Hand" – a wrench providing a comfortable working angle, better accessibility, a more secure grip, wider jaw opening and teeth with unsurpassed bite. A more refined version of the wrench is widely sought after by professionals today as the ergonomic and effective Bahco pipe wrench.
The Bahco Adjustable Wrench was his second invention, patented in 1892. It was the world’s first adjustable spanner. This was the basis for the adjustable wrench, a Swedish invention found all over the world. Since that time, well over 200 million Bahco adjustable wrenches have been sold and countless others have been manufactured by other companies once the patent expired.
Learn more about Bahco
Bahco Handsaw System
This breakthrough system features the ERGO™ handle which is interchangeable with a wide range of eight, low friction, coated, application-specific blades and launched with hand-specific sizes. The ERGO™ process and asymmetric design assure no pressure points. The handle and blade position reduce the force needed for sawing. The genius in the system is the interchangeable blade system. Users can change blades in a few seconds. Developed by testing many designs and observing users at work and launched in 2008.
We believe you should never have to adapt to the tool. Our ERGO™ tools mean you don’t have to.
Bahco is a pioneer in ergonomic hand tools. Ergonomics is the science of optimizing the interplay between people and the environment according to the principle “adapting the work to the person”. Each time you grip a tool, you put 42 different muscles to work. Using an ergonomically designed tool reduces injuries due to strain, improves productivity and, most important of all, makes work more enjoyable.
The design of ergonomic tools by Bahco is based on a scientifically-based program. This program covers facts and experiences gathered from users, ergonomists, industrial designers, research and development experts as well as extensive testing and trials together with professional end-users of the tools. The method is unique within the tool industry.
The people we use for testing are members of the Bahco End User Network (BEUN). A network of hard working professionals covering all relevant trades groups and geographical regions. The BEUN members are not on our payroll, they participate because they care about their work and because they like to be part of and influence the next generation of tools from Bahco.
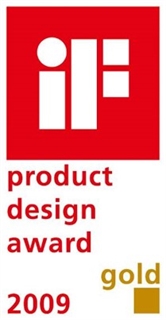
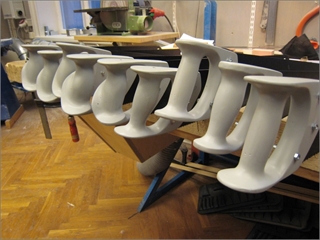
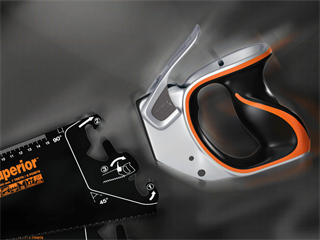
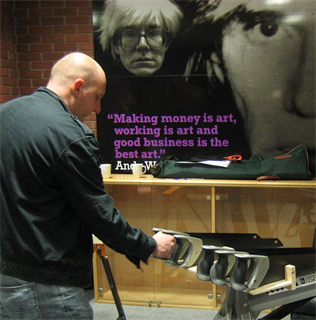
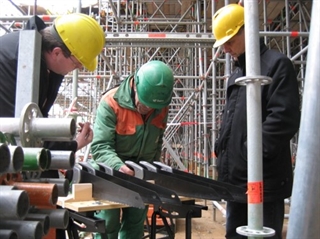
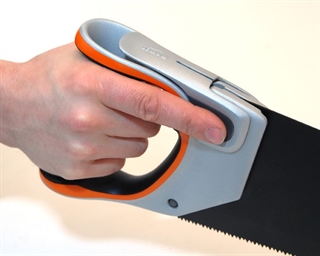
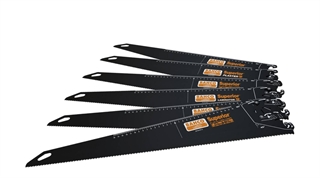
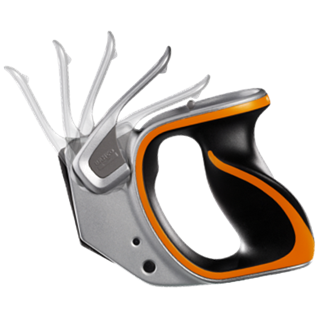
Irimo Side Nut Adjustable Wrench
Established in Urrextu, Spain in 1930 Irimo started manufacturing parts for cement factories and expanded to sophisticated tools and parts for the automotive industry. Irimo invented the side-nut adjustable wrench designed for heavy duty applications in the 1948. The unique design won a gold medal at the international Inventors Salon in Brussels in 1960. With improvements over the years, the same basic wrench offers professional users high performance for special applications today.
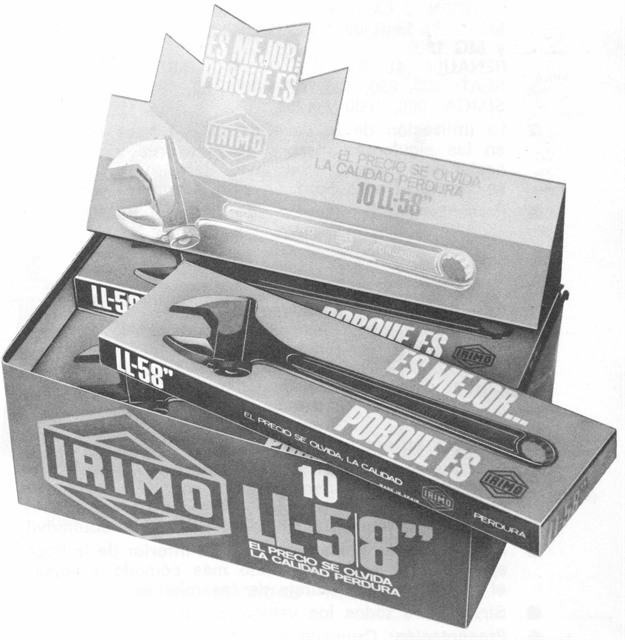

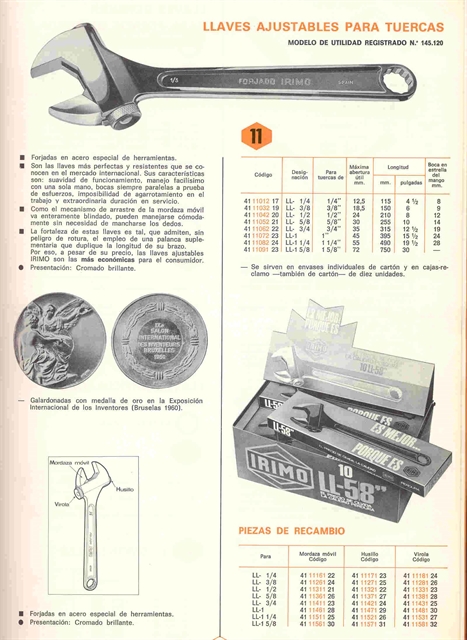
Learn more about Irimo
John Bean V3300 Wheel Alignment System
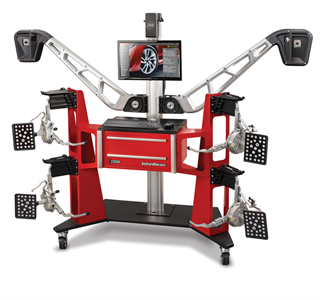
John Bean V3300 Wheel Alignment System is a leading-edge, standalone, mobile wheel alignment system that provides quick and accurate measurements so shops can perform error-free services, every time.
This tool uses an advanced camera to monitor the technician and the vehicle during the alignment process to avoid errors that could result in a bad alignment. If an error is made or there is a worn part on the vehicle, the system will stop the process and advise the technician on what the problem is before letting them invest more time in an alignment that will end with a crooked steering wheel or pulling to the left or right. If the problem is minor, the system will automatically compensate for the issue. It prevents bad alignments that result in a redo and/or an unhappy customer.
The V3300 instantly accesses real-time OEM repair information, technical service bulletins, recalls and additional data. There are no concerns about Advanced Driver Assistance Systems onboard vehicles. The aligner alerts the user when it encounters these features and provides the right procedure for adjustments and target placement.
The camera is the fastest we’ve ever offered and the optimized software flow and built-in notification system work together to provide fast and accurate readings. This permits the technician to work quickly, while maintaining confidents that the results will be correct.
Learn more about John Bean
John Bean B2000P Diagnostic Wheel Balancer
The John Bean B2000P Diagnostic Wheel Balancer is a sophisticated balancer that offers touchless measurement and analysis. Automatic inputs remove the opportunity for error.
This advanced balancer uses an array of digital cameras to fully scan the tire and the outer rim. It creates a 3D model of sidewalls and tread surface and analyses this for potential problems. Then, it notifies the technician of these problems.
This 3D model is automatically analyzed for tread depth, flat spots, punctures, bent rim, and bead seating. The technician is shown the areas that have problems so they can solve or replace the tire and/or wheel. It takes the judgement away from these repairs and reduces them to measurable cases.
Learn more about John Bean
Lindström High-Precision Cutters and Pliers
Mitchell 1 SureTrack
Mitchell 1 SureTrack is a software solution that is part of the ProDemand repair information product or in more capable Snap-on diagnostic units. It uses a proprietary database of one billion actual repairs to help professional automotive technicians diagnose and repair vehicle problems. SureTrack Community is an interactive tool to use to collaborate with other professionals to solve tricky diagnostic problems.
SureTrack searches using common words. It speeds the repair process and it provides real confidence in the diagnosis.
The SureTrack Community gives technicians access to thousands of professional automotive technicians across North America. They not only get help with difficult vehicle questions but can contribute to the community by answering other technicians’ questions and share tips for vehicle diagnostics and repair.
The community includes a robust automated notification and subscription system which helps obtain answers to questions quickly, typically within a few minutes. The community has many members who monitor questions for particular vehicle lines to ensure that the questions get answered quickly. Once the vehicles is repaired, techs are encouraged to log in the fix which then becomes part of the greater SureTrack data system to help future technicians who may come across the same issue.
SureTrack also makes the ProView feature accessible for all users. ProView shows relationships between codes, symptoms and components, and can be especially valuable when diagnosing multiple trouble codes at the same time.
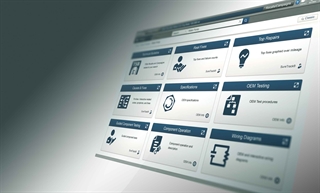
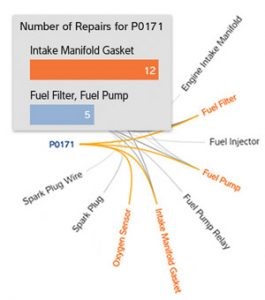
Learn more about Mitchell 1
Norbar EvoTorque Tool
This powerful new innovation combines several company division technologies in a single tool and was made possible by Norbar joining the family. This highly capable tool for heavy industry combines a new battery powered brushless motor, data memory and transfer capabilities, with proven gearboxes to deliver a line of accurate, efficient, intelligent battery torque tools.
The EvoTorque® is an electronic torque tool designed for applying torque to threaded fasteners. The unique ‘Intelligent Joint Sensing’ technology will accurately tighten to the correct torque without the risk of excess overshoot or undershoot that is common in other electric tools.
Norbar was created from wartime need converted to universal demand. Incorporated in 1943, the "North Bar Tool Company" became the first company in Britain to commercially manufacture torque wrenches. The initial demand was driven by the need for the gasket-less cylinder head of the Rolls Royce Merlin engine used in WWII Spitfires and P-515’s to be accurately tightened. The original Norbar Ratchet Adjustable Torque Wrench was the tool that did the job.
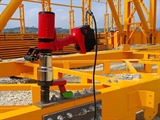
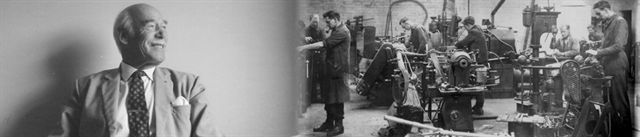
Learn more about Norbar
Sturtevant Richmont Error Proofing Torque Solution
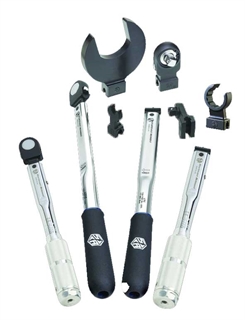
Because most torque tools are controlled by a user, they’re making them susceptible to human error. But many critical industries demand an error-free fastening process. Sturtevant Richmont solutions address the need for error proofing with innovations like process controller technology that organizes and directs workers’ tools and tasks, while creating custom solutions for many operations.
Error proofing is about eliminating variables that cause errors. Sturtevant Richmont has designed every torque solution to help overcome this. They build error proofing into each and every single tool. The systematic approach has long leaned on these approaches:
Error Proofing By Design – Design tools to reduce or eliminate the human influence in the torque application and torque testing process.
Error Proofing By Behavior Modification – They firmly believe that people want to do a good job at their craft. These tools help provide behavior modification much like a coach would provide.
Error Proofing By Guidance – All assemblies require some type of operator guidance. Some are simple while some are complex. It is simple feedback letting an operator know that the fastener is not compliant. Or guidance can come in the form of ensuring that the right tool for the job is selected, used properly, and returned to the appropriate place in the tool tray.
These three approaches all work in conjunction with each other. In some cases, there may be only one of the error proofing approaches. In most cases, two or even all three of the error proofing approaches find their way into a tool.
Learn more about Sturtevant Richmont